Home » The Impact of Switching Packaging Suppliers
The Impact of Switching Packaging Suppliers
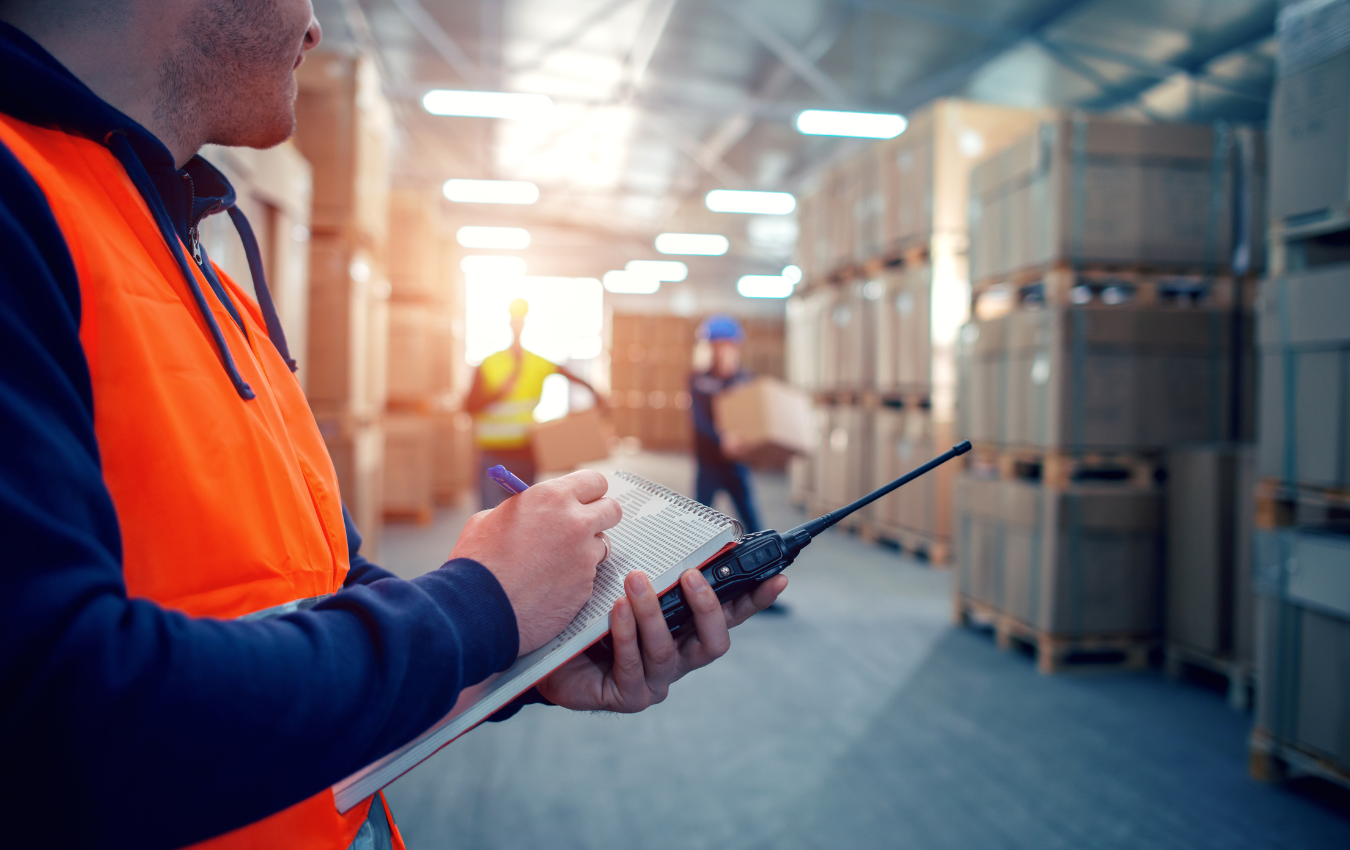
For businesses, the decision to change packaging suppliers can be driven by various factors such as cost, quality, service, or the need for innovation. However, this change, while potentially beneficial, can also significantly affect the outcome of your product’s packaging. In this detailed blog, we’ll explore the various aspects of how switching packaging suppliers can impact your product and what to consider during this transition.
Understanding the Implications of Changing Suppliers
The decision to switch packaging suppliers is not one to be taken lightly. It involves considering how the change will impact the quality, design, cost, and overall brand consistency of your product’s packaging.
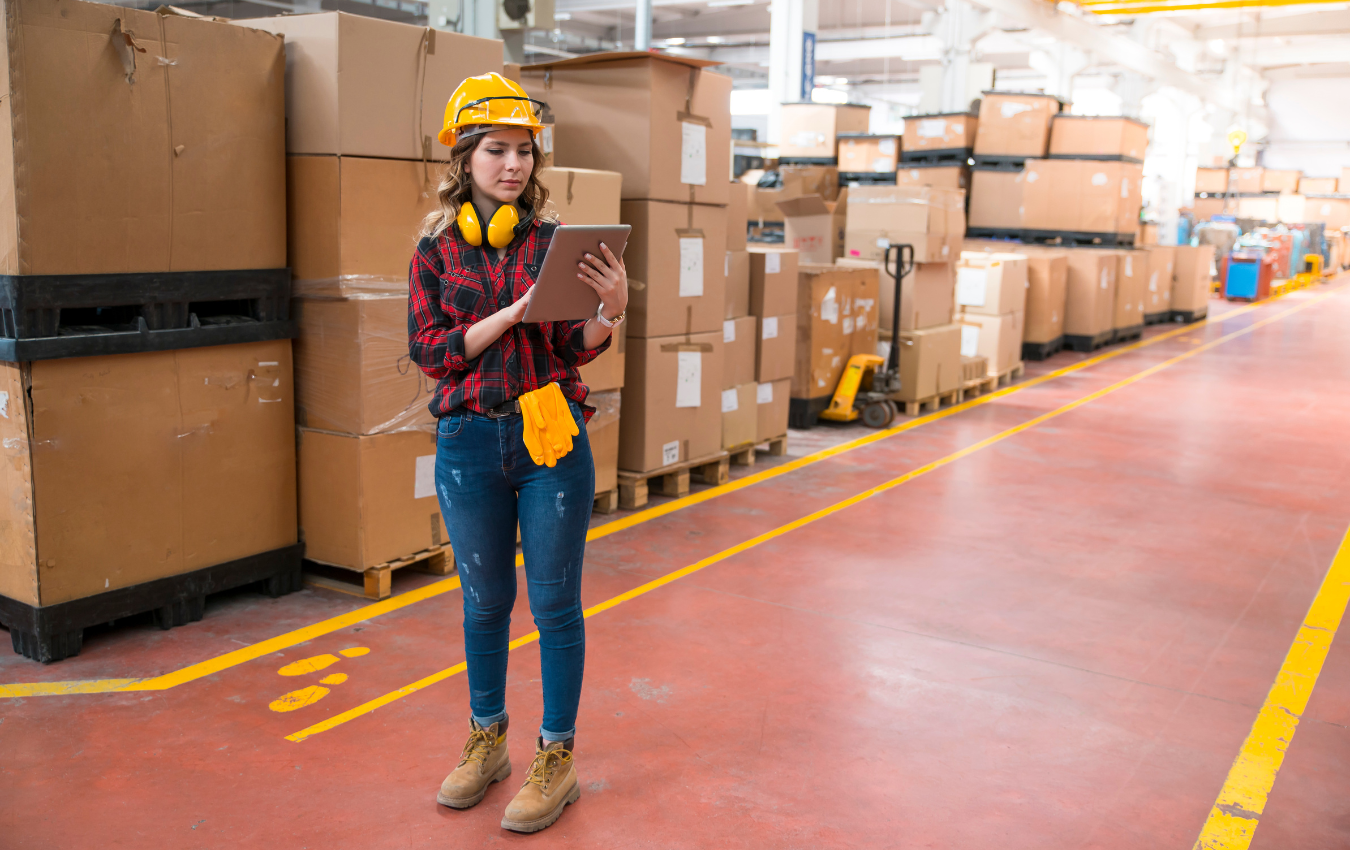
Potential Benefits of Changing Suppliers
- Improved Quality and Innovation:
- A new supplier might offer better quality materials or more innovative packaging solutions that enhance the aesthetic and functionality of your product.
- Access to the latest technology and packaging trends can give your product a competitive edge in the market.
- Cost Reduction:
- Switching suppliers can be financially beneficial if the new supplier offers more competitive pricing without compromising quality.
- Cost savings can also come from more efficient production processes or economies of scale.
- Enhanced Sustainability:
- A new supplier may provide more eco-friendly packaging options, aligning with modern sustainability trends and consumer preferences.
Challenges and Risks of Supplier Transition
- Inconsistency in Packaging Quality:
- A new supplier may interpret your specifications differently, leading to variations in quality or appearance of the packaging.
- Ensuring consistency is critical, especially if the packaging is a key component of your brand identity.
- Transition Delays and Logistics:
- Switching suppliers can lead to transition delays. Timing is crucial, especially if you have strict product launch timelines.
- Navigating the logistics of the switch, including winding down with the current supplier and ramping up with the new one, requires careful planning.
- Communication and Misunderstandings:
- Establishing effective communication with a new supplier is vital. Misunderstandings can lead to errors in the packaging production.
- Clear and detailed discussions about your packaging needs and expectations are essential.
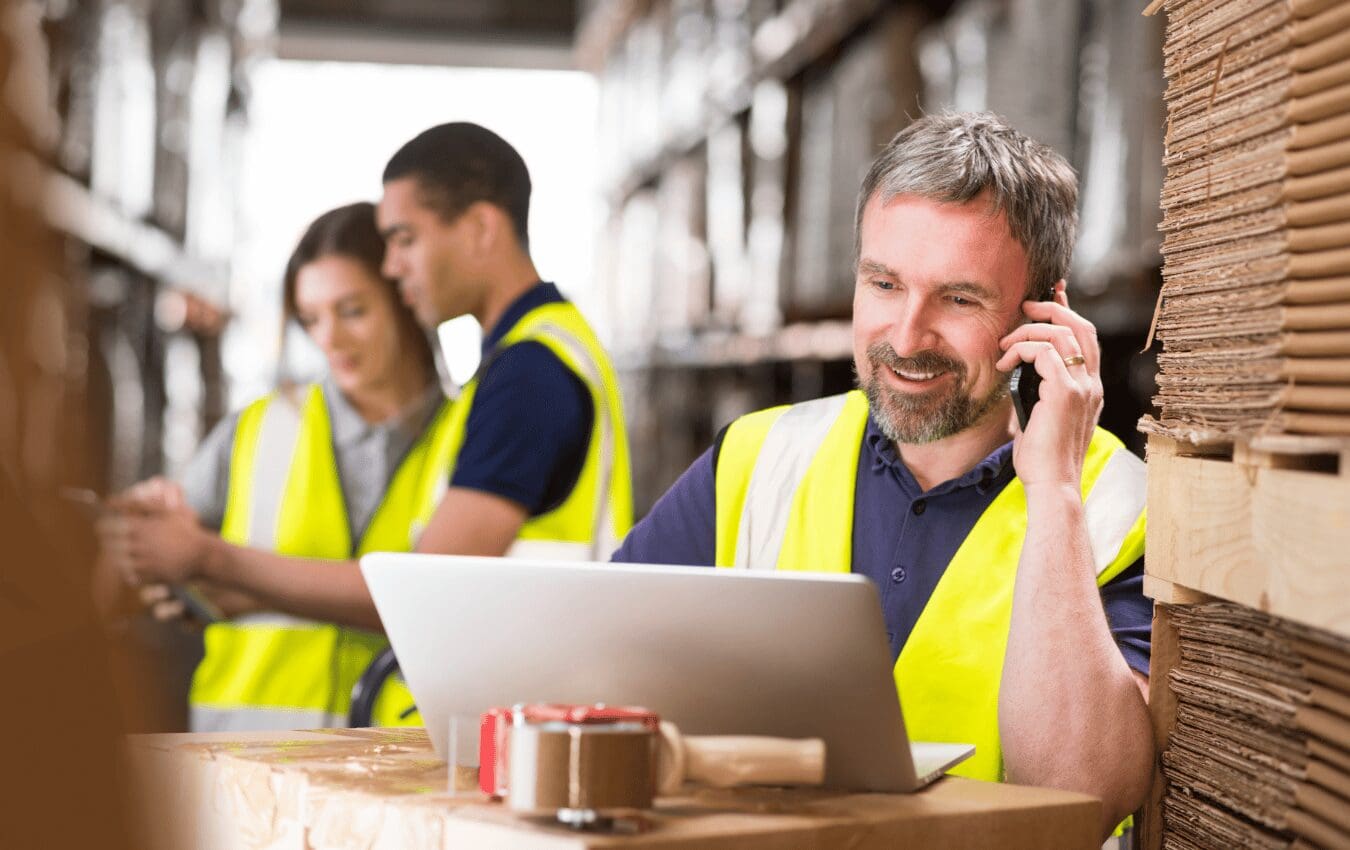
Steps to Ensure a Smooth Transition
- Conduct Thorough Research:
- Before switching, research potential suppliers thoroughly. Look for reviews, request samples, and evaluate their customer service and reliability.
- Consider suppliers’ expertise in your specific product category.
- Risk Assessment:
- Conduct a risk assessment to understand the potential impacts of switching suppliers.
- Plan for contingencies in case of unexpected challenges during the transition.
- Clear Communication of Specifications:
- Provide detailed specifications, brand guidelines, and quality standards to your new supplier.
- If possible, share examples of previous packaging that met your standards.
- Quality Control Measures:
- Implement stringent quality control processes with the new supplier to ensure packaging meets your standards.
- Regularly review sample batches before approving full-scale production.
- Building a Strong Partnership:
- Foster a collaborative relationship with your new supplier. Mutual understanding and trust are key to a successful partnership.
- Regular meetings and open lines of communication can help align expectations.
- Gradual Transition and Testing:
- Consider a phased approach to the transition, starting with smaller batches.
- Test the market’s reaction to the new packaging before fully committing to the change.
If you are interested in making the switch, then partner with Brown Packaging today to get started.
Why Co-Packaging Becomes Critical During the Holidays As the holiday season approaches, packaging teams are under pressure to deliver high volumes of promotional sets, combo
Holiday demand starts long before December. So should your packaging. For B2B and D2C brands alike, Q4 is the most critical—and most chaotic—shipping window of
The Challenge of Multi-SKU Holiday Programs During the holiday season, brands often shift from selling single products to curated sets, bundled assortments, and promotional kits—each
Rigid boxes are the gold standard of premium packaging. Whether used for cosmetics, electronics, fashion, or high-end subscription kits, rigid boxes do more than protect
Understanding One-Piece FOL and Three-Piece Bike Shipping Boxes Choosing the right box style is essential when shipping bicycles—especially for brands, manufacturers, and distributors focused on
Corrugated boxes are essential to shipping, retail, and e-commerce—but when you introduce custom printing, the stakes (and the opportunities) rise. Print isn’t just about looks—it’s
Home » The Impact of Switching Packaging Suppliers
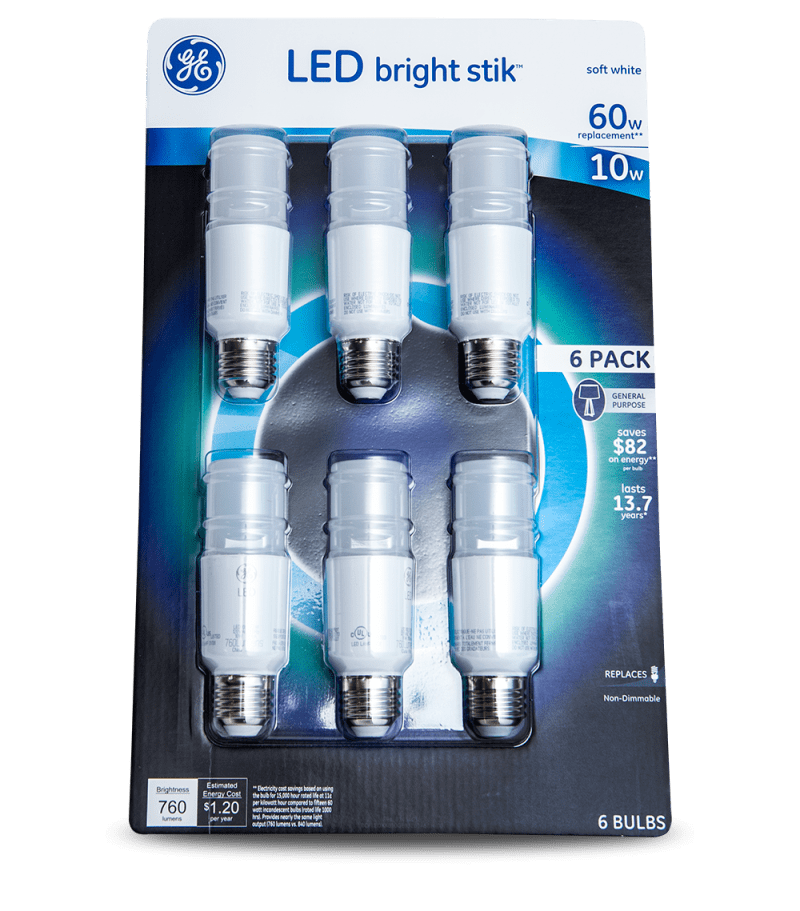
In the world of packaging, different products require different packaging solutions. With myriad options available today, companies can be selective about which suits their needs
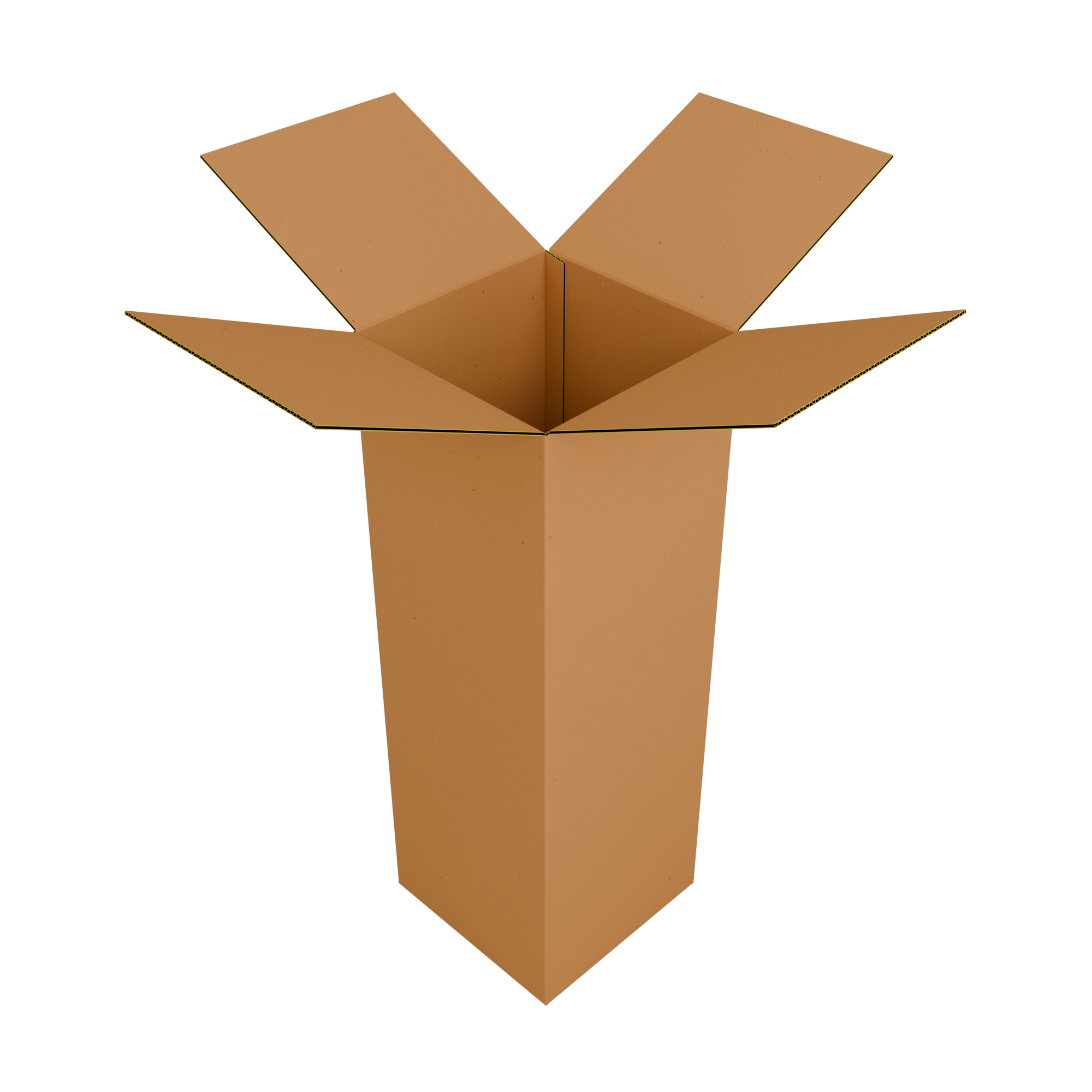
Designing a Full-Overlap (FOL) box tailored to your specific needs is a critical step in ensuring the safe and secure packaging of your products. FOL
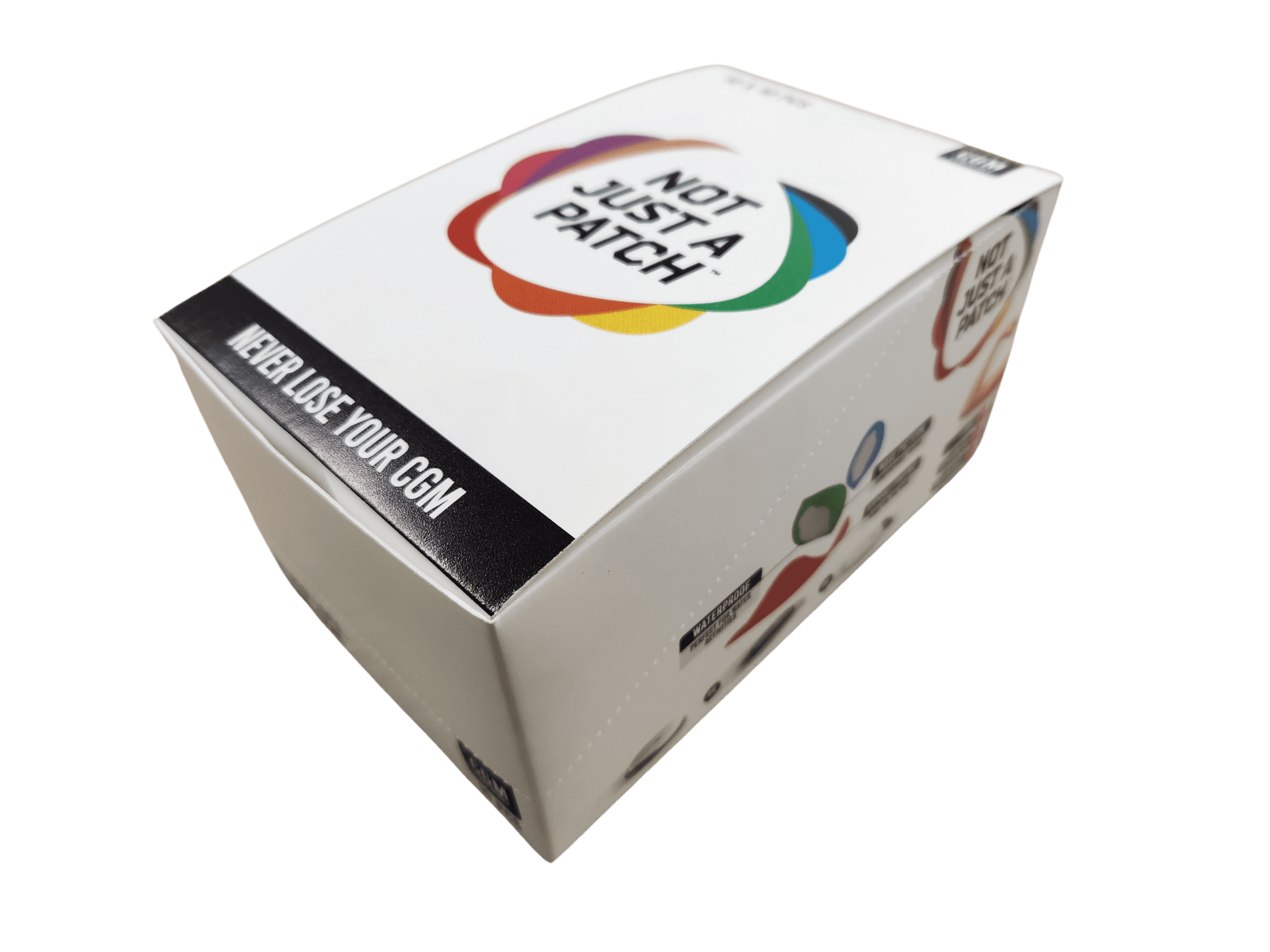
In today’s market, the printing strategy employed on packaging can play a significant role in a product’s success. This guide is tailored to help buyers