Home » How Packaging Lead Times Influence Shipping Costs
How Packaging Lead Times Influence Shipping Costs
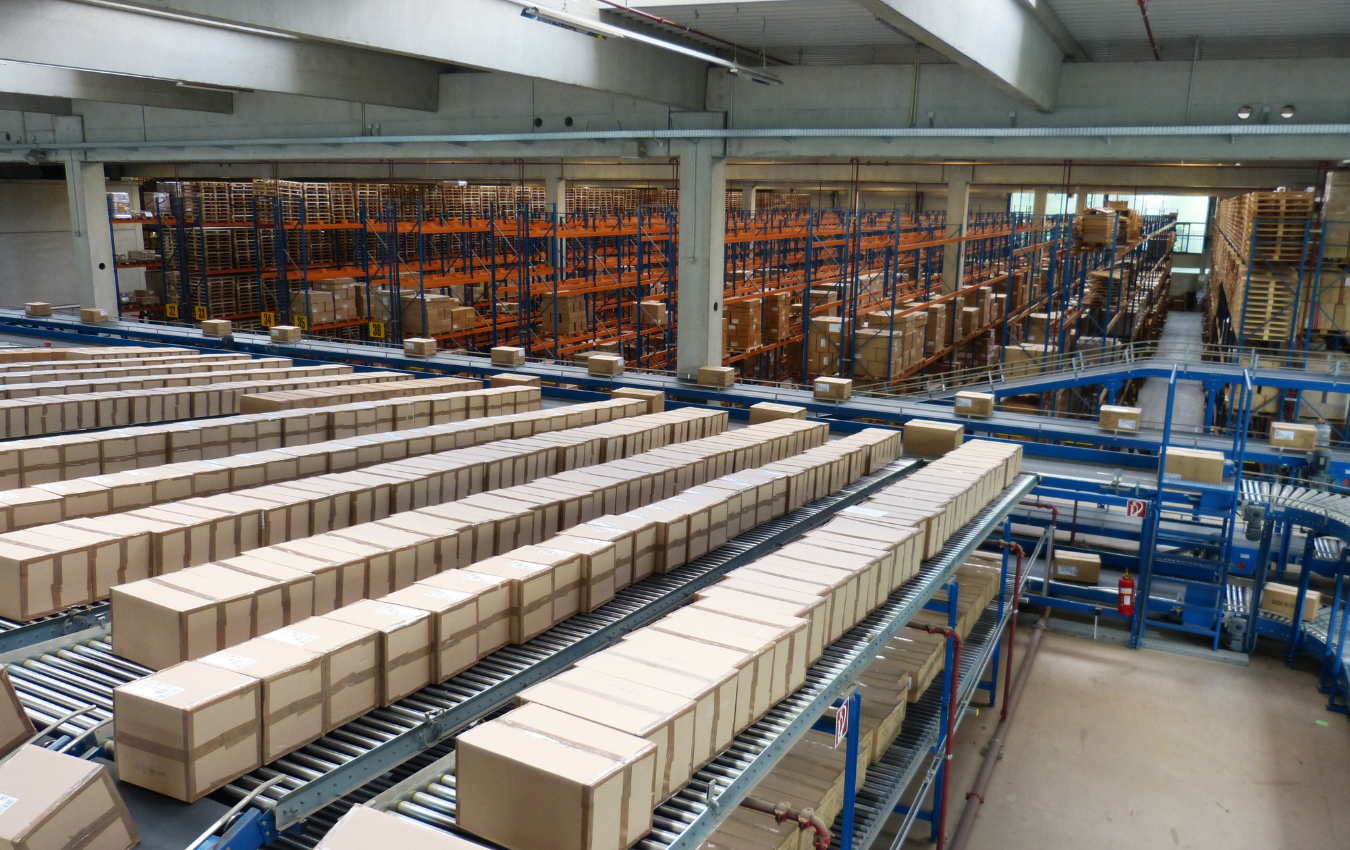
In the world of logistics and supply chain management, the cost of shipping plays a pivotal role in determining a company’s profitability. While factors like distance, weight, and shipping method undoubtedly influence shipping costs, one often overlooked aspect is packaging lead times. Packaging lead times refer to the amount of time it takes for a product to be prepared, packaged, and ready for shipment. In this blog, we will delve into the intricate relationship between packaging lead times and shipping costs, and how businesses can optimize this crucial element of their operations.
Understanding Packaging Lead Times
Before we delve into the impact of packaging lead times on shipping costs, it’s essential to understand what packaging lead times entail:
- Product Preparation: This involves getting the product ready for shipment. It includes quality checks, labeling, and any necessary assembly or disassembly.
- Packaging: Once the product is prepared, it needs to be securely and appropriately packaged to ensure it arrives at its destination intact. Packaging materials, like boxes, bubble wrap, and pallets, need to be sourced and utilized.
- Documentation: Preparing the required shipping documents, including customs paperwork and shipping labels, is a crucial part of packaging lead times.
- Storage: If products are not shipped immediately, they must be stored safely and efficiently, incurring storage costs.
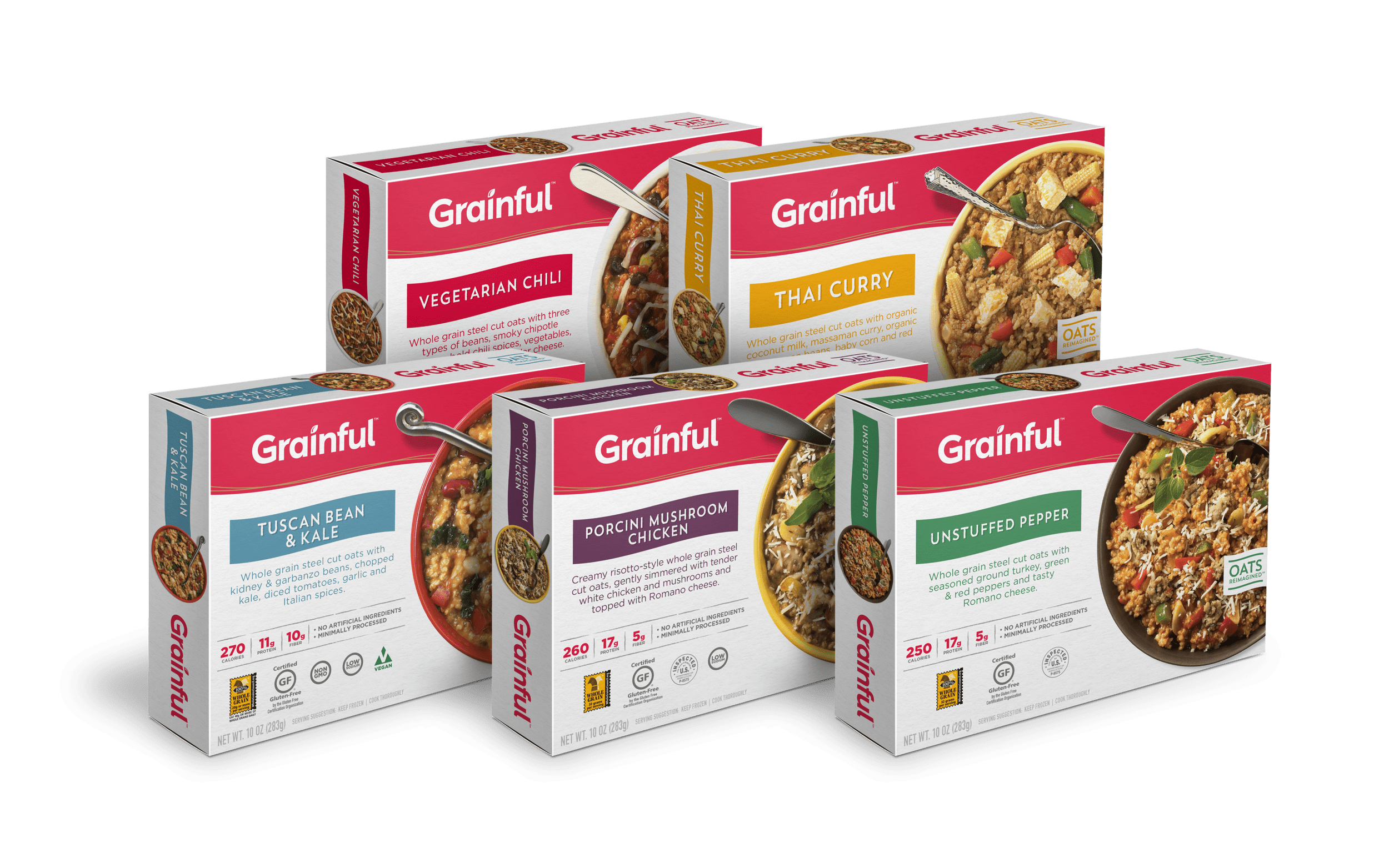
How Packaging Lead Times Impact Shipping Costs
- Inventory Holding Costs: The longer products sit in storage due to extended packaging lead times, the higher the inventory holding costs become. This includes warehousing fees, insurance, and depreciation of the stored goods. These costs can add up significantly over time.
- Shipping Mode Selection: Companies often choose shipping modes based on the urgency of delivery. Air freight, which is faster but more expensive, may be chosen when packaging lead times are short. Conversely, when lead times are extended, less expensive options like sea freight may be preferred.
- Rush Orders: In some cases, rushed packaging to meet tight delivery deadlines can result in higher labor and material costs, potentially impacting overall shipping costs.
- Space Utilization: Efficient packaging lead times allow for better space utilization in containers or trucks. Products that are poorly packaged or not properly consolidated may require more space and lead to additional transportation costs.
- Consolidation Opportunities: Longer packaging lead times provide opportunities to consolidate shipments. Combining several smaller shipments into one larger shipment can be more cost-effective, as it reduces the cost per unit transported.
- Customs and Compliance: Adequate packaging lead times enable companies to complete all necessary customs and compliance documentation accurately. Rushed processes may lead to errors and fines, increasing overall shipping costs.
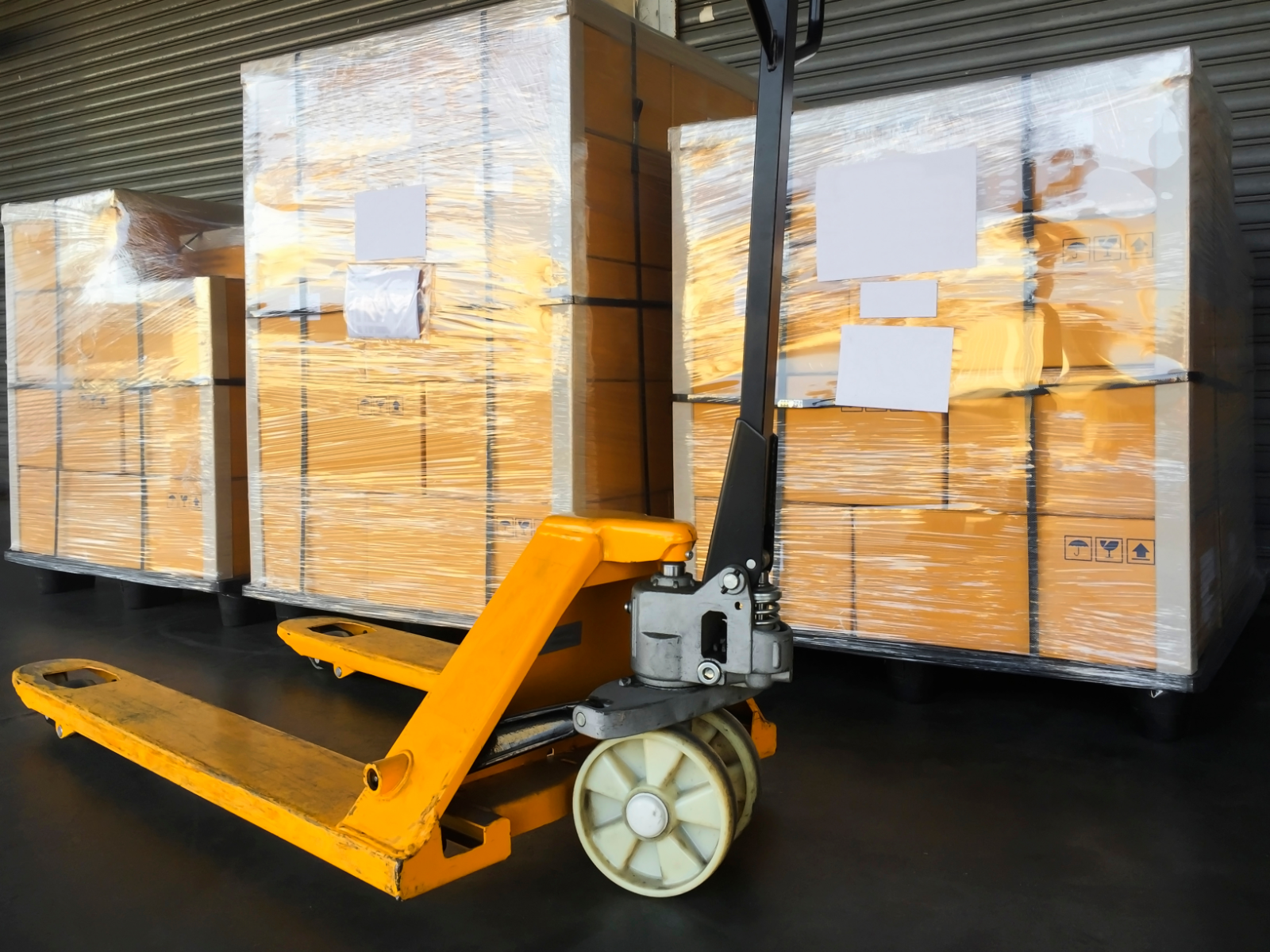
Optimizing Packaging Lead Times
- Forecasting: Accurate demand forecasting is crucial for planning packaging lead times effectively. Companies should use historical data, market trends, and customer orders to predict packaging requirements.
- Efficient Packaging Processes: Streamline and optimize your packaging processes to reduce lead times without compromising on quality. Automation and lean principles can be valuable in achieving this.
- Communication: Collaborate closely with suppliers and logistics partners to align packaging lead times with transportation schedules. Clear communication can help avoid unnecessary delays.
- Inventory Management: Do not run out of supplies by keeping enough with demand and maintaining a safety stock.
- Contingency Planning: Develop contingency plans for unexpected delays or spikes in demand. These plans can help maintain customer satisfaction while mitigating additional shipping costs.
Conclusion
Packaging lead times are a critical factor in determining shipping costs. An efficient packaging process not only reduces the time products spend in storage but also enables better transportation planning. By understanding and optimizing packaging lead times, businesses can not only reduce their shipping costs but also enhance their overall supply chain efficiency and customer satisfaction. In today’s highly competitive market, these factors can make a significant difference in a company’s success.
If you are interested in packaging products, then partner with Brown Packaging today to get started.
Rigid boxes are the gold standard of premium packaging. Whether used for cosmetics, electronics, fashion, or high-end subscription kits, rigid boxes do more than protect
Understanding One-Piece FOL and Three-Piece Bike Shipping Boxes Choosing the right box style is essential when shipping bicycles—especially for brands, manufacturers, and distributors focused on
Corrugated boxes are essential to shipping, retail, and e-commerce—but when you introduce custom printing, the stakes (and the opportunities) rise. Print isn’t just about looks—it’s
When it comes to shipping bikes, selecting the right type of corrugated box is essential to ensure product protection, ease of handling, and cost efficiency.
Before committing to a full production run, businesses often receive packaging samples to evaluate fit, functionality, print quality, and overall design. Whether it’s a digital
Choosing the right corrugated box size is crucial for product protection, shipping efficiency, and cost savings. Whether you’re packing a single item or multiple products,
Home » How Packaging Lead Times Influence Shipping Costs
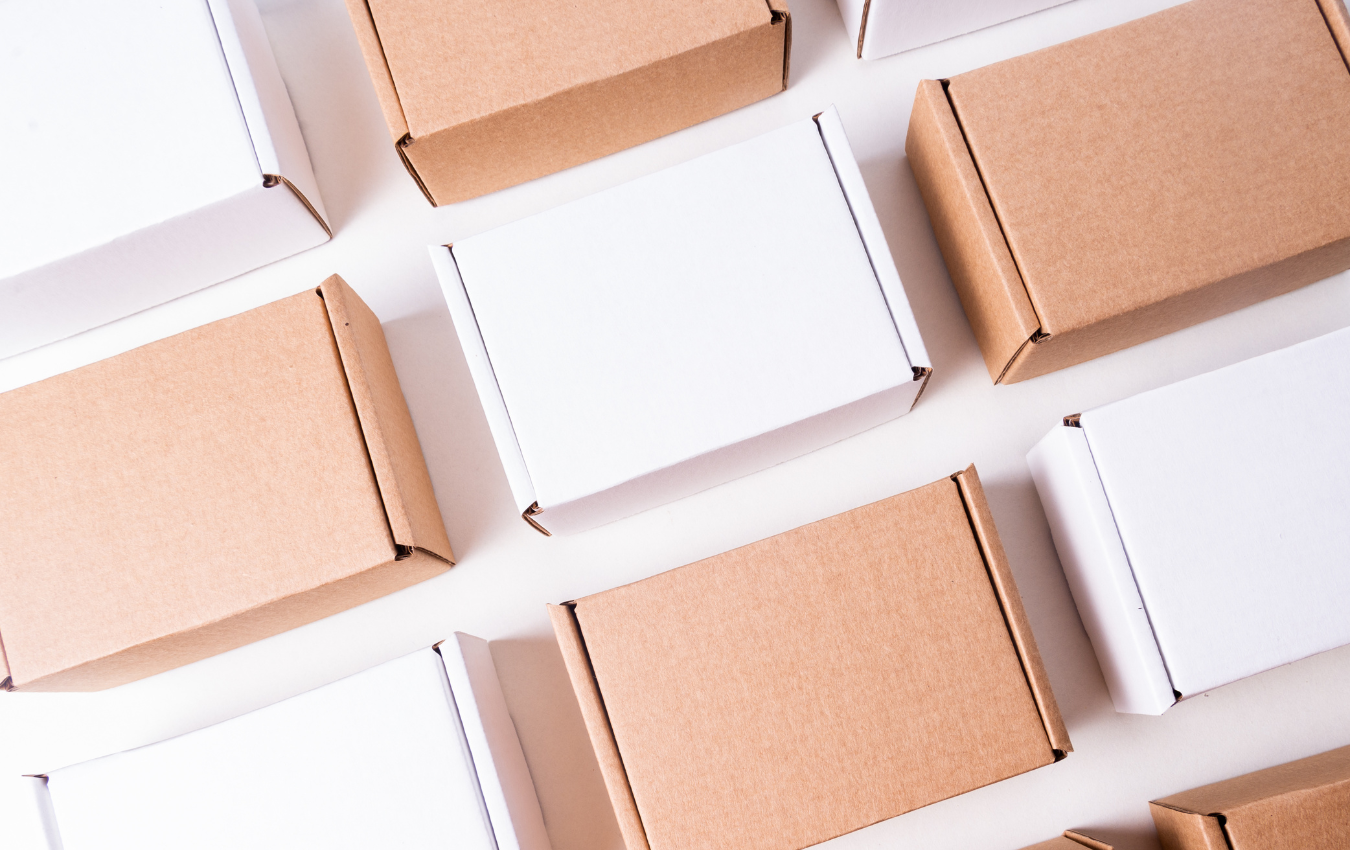
When it comes to packaging solutions, corrugated boxes are at the forefront of industry choices, providing durability, flexibility, and sustainability. However, the debate often arises
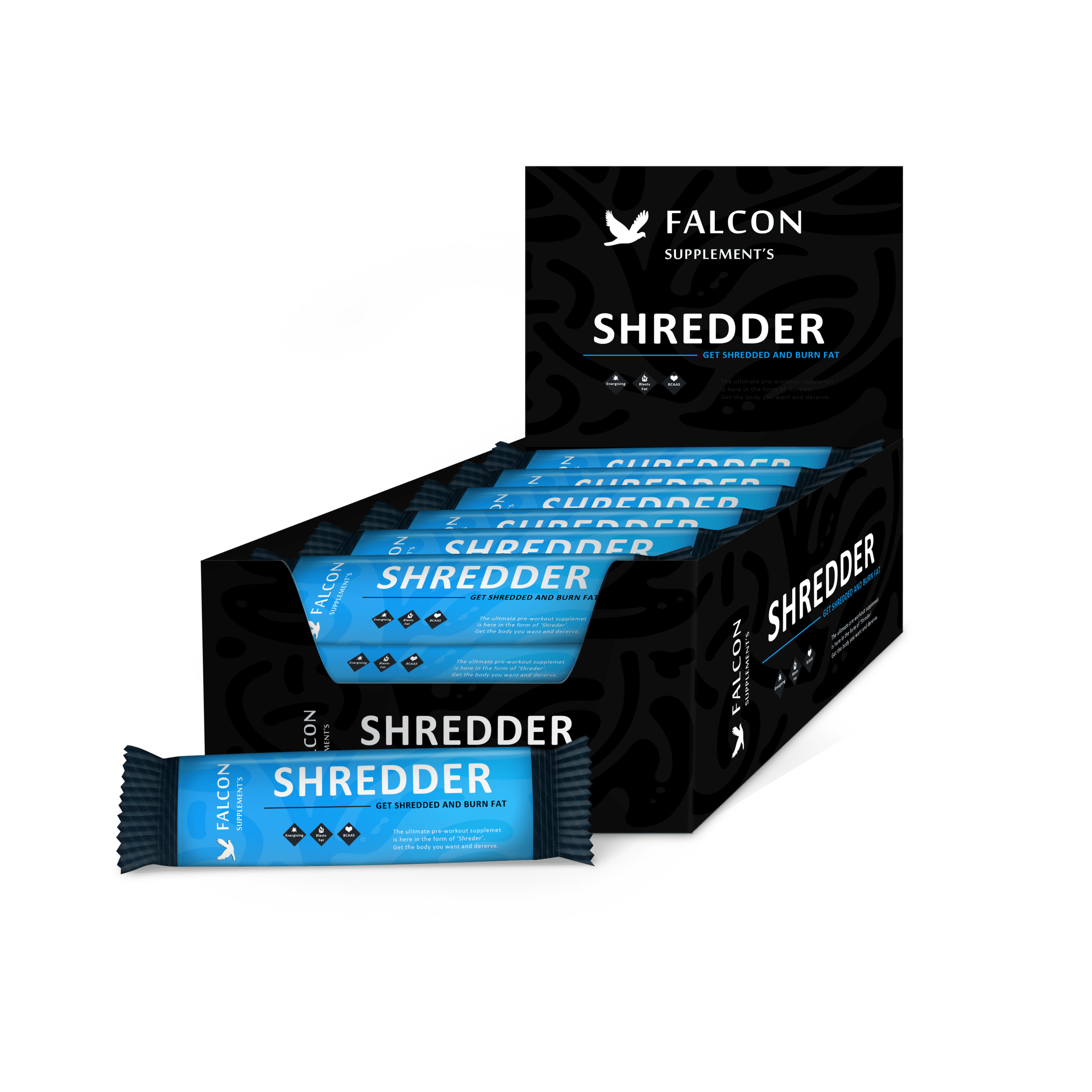
In an increasingly competitive marketplace, the role of packaging extends beyond the first point of sale – it’s a vital tool in fostering customer loyalty
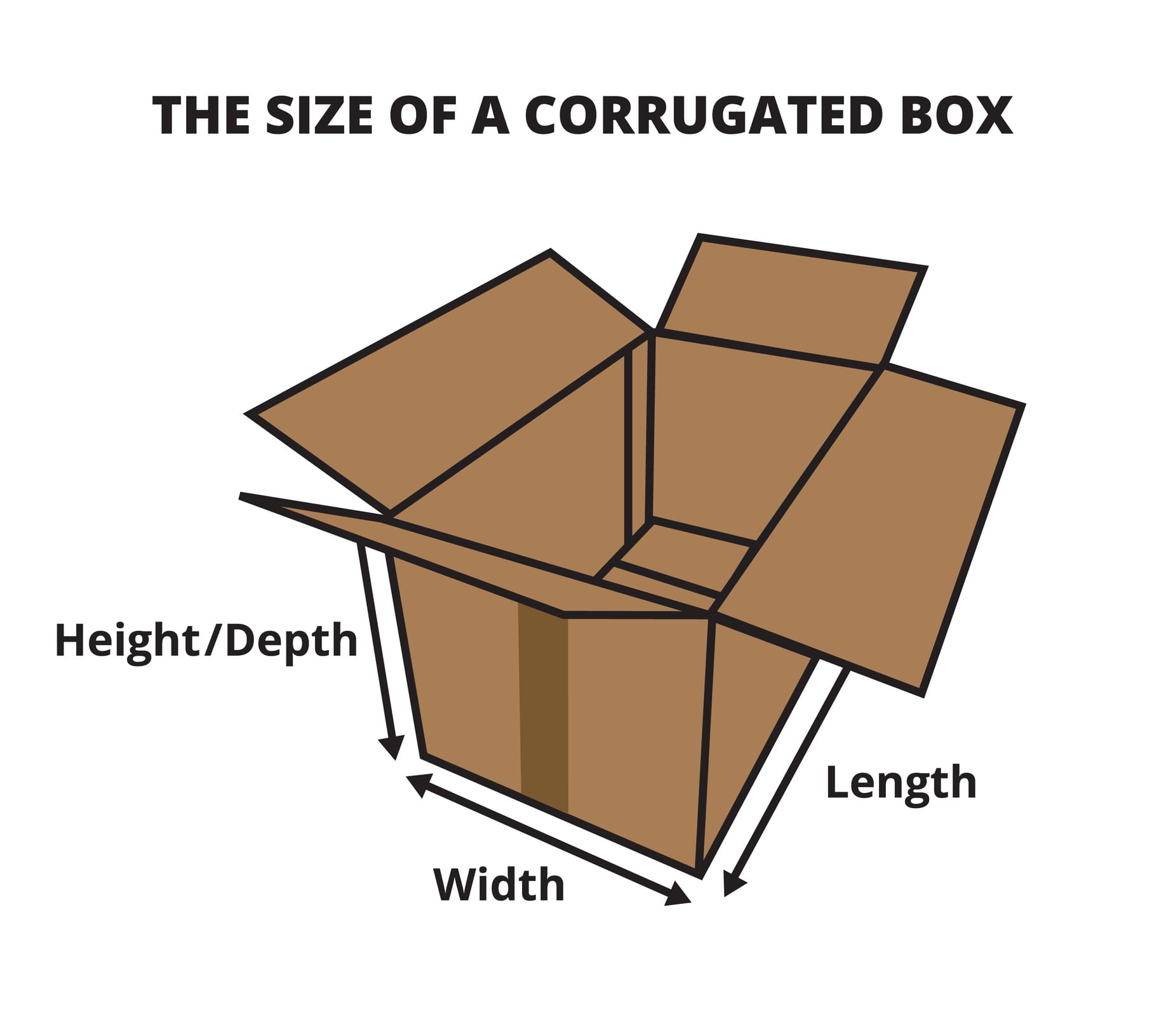
Structurally designing your corrugated box involves understanding the specific requirements of your product and applying principles of material science and engineering to ensure optimal protection,