Home » Corrugated Product Manufacturing Methods
Corrugated Product Manufacturing Methods
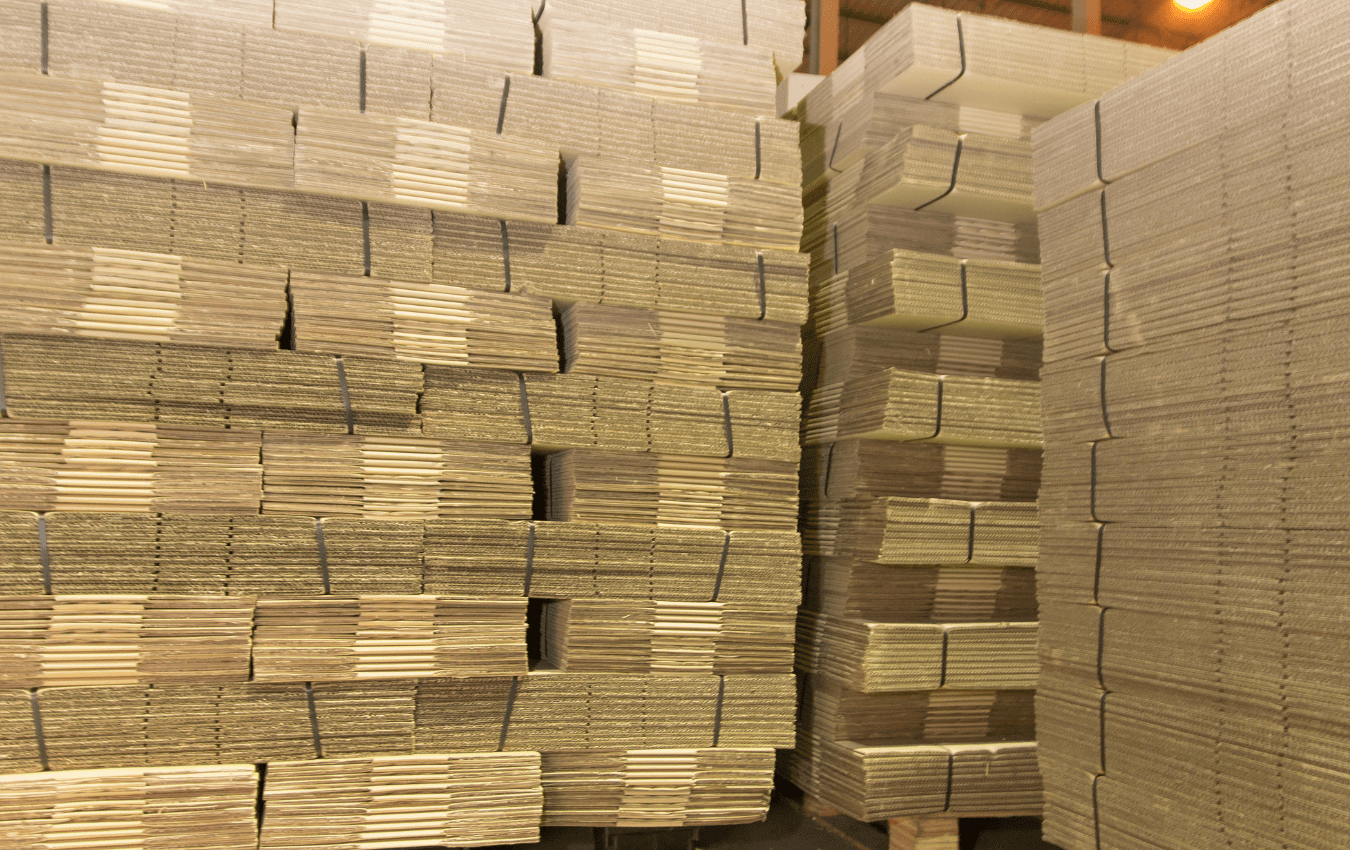
When you see packaging, you don’t see the process it went through, you just see the result. It is important to understand how each package is created, especially if you are looking for packaging for your business.
The two most common manufacturing processes include flexo folder gluer and die cutting. Flexo folder gluer is best used for certain style boxes, mainly used for shipping. While die cut is best used for custom boxes, such as mailers and inserts. One of the main differences between these methods is the requirement for tooling. Flexo folder gluer can operate without a tool, whereas die cut products will require specific tooling depending on the style of the box.
To make the best choice for your business needs, you must understand the differences between the machines.
Machine Run:
What is flexo folder gluer?
The flexo folder gluer is a machine that produces boxes with a wide range of configurations available to suit any production level. It can produce boxes without requiring a tool. This system prints, scores and slots the boxes before folding and gluing them together. Although this machine is full-service, it can only make certain styles of boxes.
Styles that can be made with this machine:
RSC- Regular slotted container
HSC- Half slotted container
FOL- Full overlap
POL- Partial overlap
The main elements of flexo folder gluer:
- Feeder: stacks and squares the boards before moving into the machine at the required speed
- Flexographic print units: one for each color
- Creasing and slotting units: cut and score the boards, to create flaps and panels
- Folder gluer: apply adhesive to the glue tab and fold
- Counter ejector: stacks the boxes in the required quantities according to the thickness of the material.
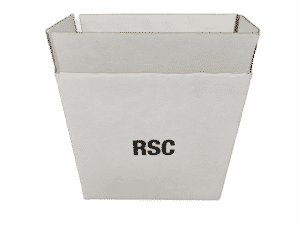

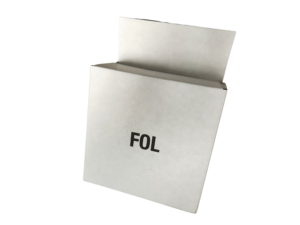
Die Cut:
What is die cutting?
Die cutting is a process that transforms material by cutting, forming, and shearing it into custom shapes and designs. This machine requires tools and uses rollers and cutting plates to put pressure on a die to push through and create a precise die cut. If you are ordering specific style boxes, then you will need to use a die cut machine. There is two important kinds of die cutting; flatbed and rotary.
Flatbed die cutting-
Flatbed die cutting cuts the desired shape out of material using a hydraulic flatbed press. This works well for low volume projects of consistent cut or larger sized products.
Advantages:
- Lower tooling cost
- Max tonnage pressures
- Process thicker materials in larger and wider sizes
Disadvantages:
- Slower
- Price per piece is more expensive
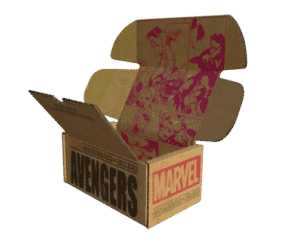
Rotary die cutting-
Rotary die cutting uses a cylindrical die to cut shapes out of material. These cylinders are fully covered in blades to cut out the desired shape as it moves around in a circular motion. This machine cuts a wide range of designs with the highest degree of precision and accuracy.
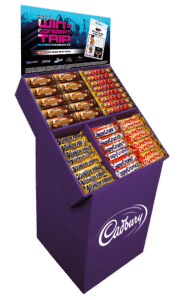
Advantages:
- Consistent cutting speeds and precision
- Faster production
- High volume productions
Disadvantages:
- Tooling is more expensive
- Stricter size constraints
Summary Machine Run vs Die Cut:
Selecting between machine run and die cut just comes down to what kind of packaging your business needs. The main determining factor between choosing machine run or die cut depends on the style and if a tool is required to cut the boxes. If it is a specific style or shaped box and a tool is needed to cut the boxes, then die cut would be the best option. If no tools are required, then machine run would be the best option. Machine run only makes certain style of boxes which are mainly used for shipping purposes, if any other style is needed then you must use a die cut machine.
Each process has its advantages and disadvantages, it is just important to decide which will work best for your business packaging needs. If unsure of which process is needed for your business, contact Brown Packaging today to speak with one of our packaging specialists.
Why Board Grade Selection Matters In today’s volatile supply chain environment, packaging failures aren’t just a nuisance—they’re a liability. Damage in transit, product returns, and
Why Holiday Fulfillment Demands Precision The holiday season introduces a unique set of pressures across the packaging and supply chain landscape—especially for businesses managing kitting,
Why Custom Corrugated Boxes Remain a 2026 Essential Custom corrugated boxes continue to be the most relied-on packaging solution for industries ranging from industrial manufacturing
Why Co-Packaging Becomes Critical During the Holidays As the holiday season approaches, packaging teams are under pressure to deliver high volumes of promotional sets, combo
Holiday demand starts long before December. So should your packaging. For B2B and D2C brands alike, Q4 is the most critical—and most chaotic—shipping window of
The Challenge of Multi-SKU Holiday Programs During the holiday season, brands often shift from selling single products to curated sets, bundled assortments, and promotional kits—each
Home » Corrugated Product Manufacturing Methods
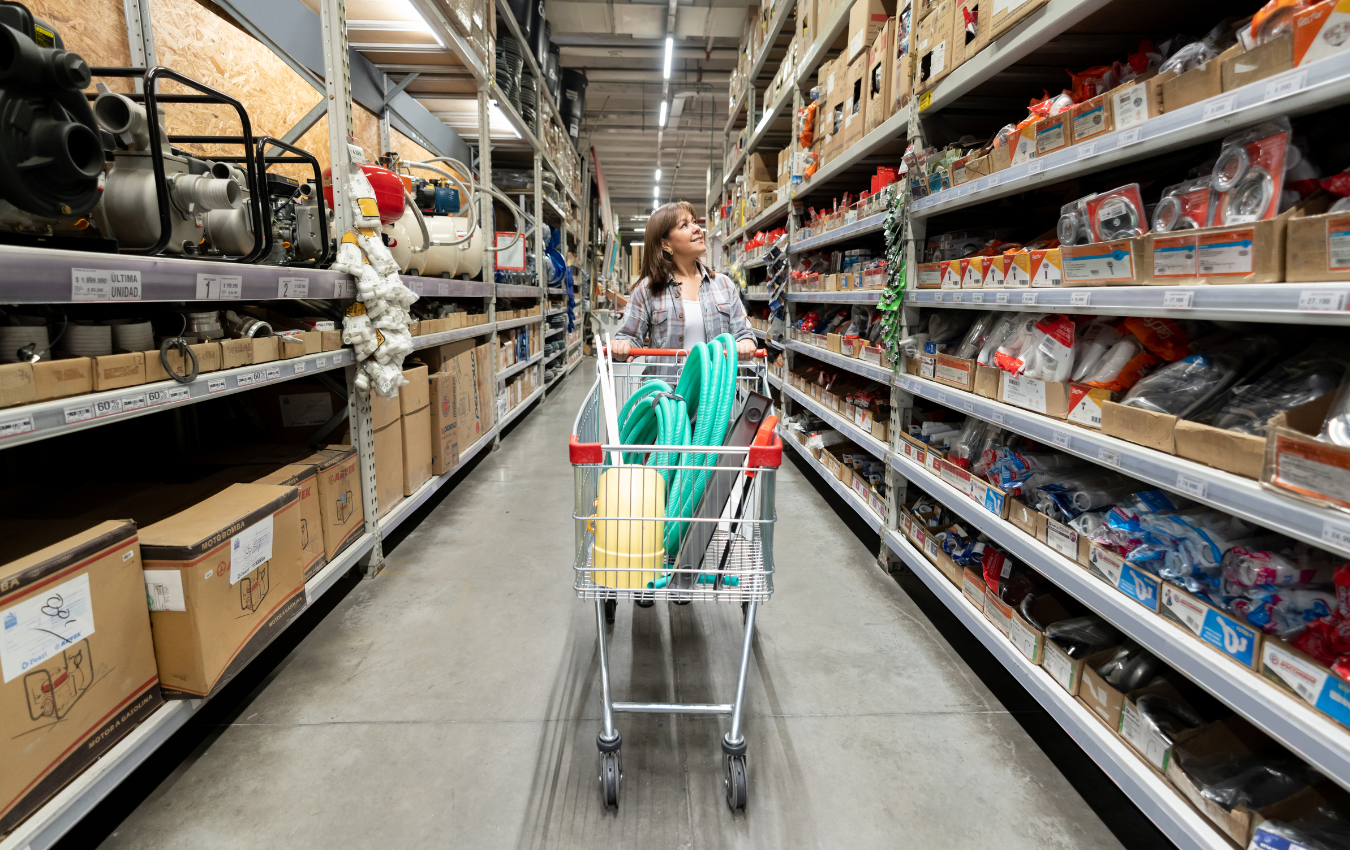
For those uninitiated in the finer points of storage and organization, corrugated bin boxes might sound like an odd focal point. However, for hardware stores,
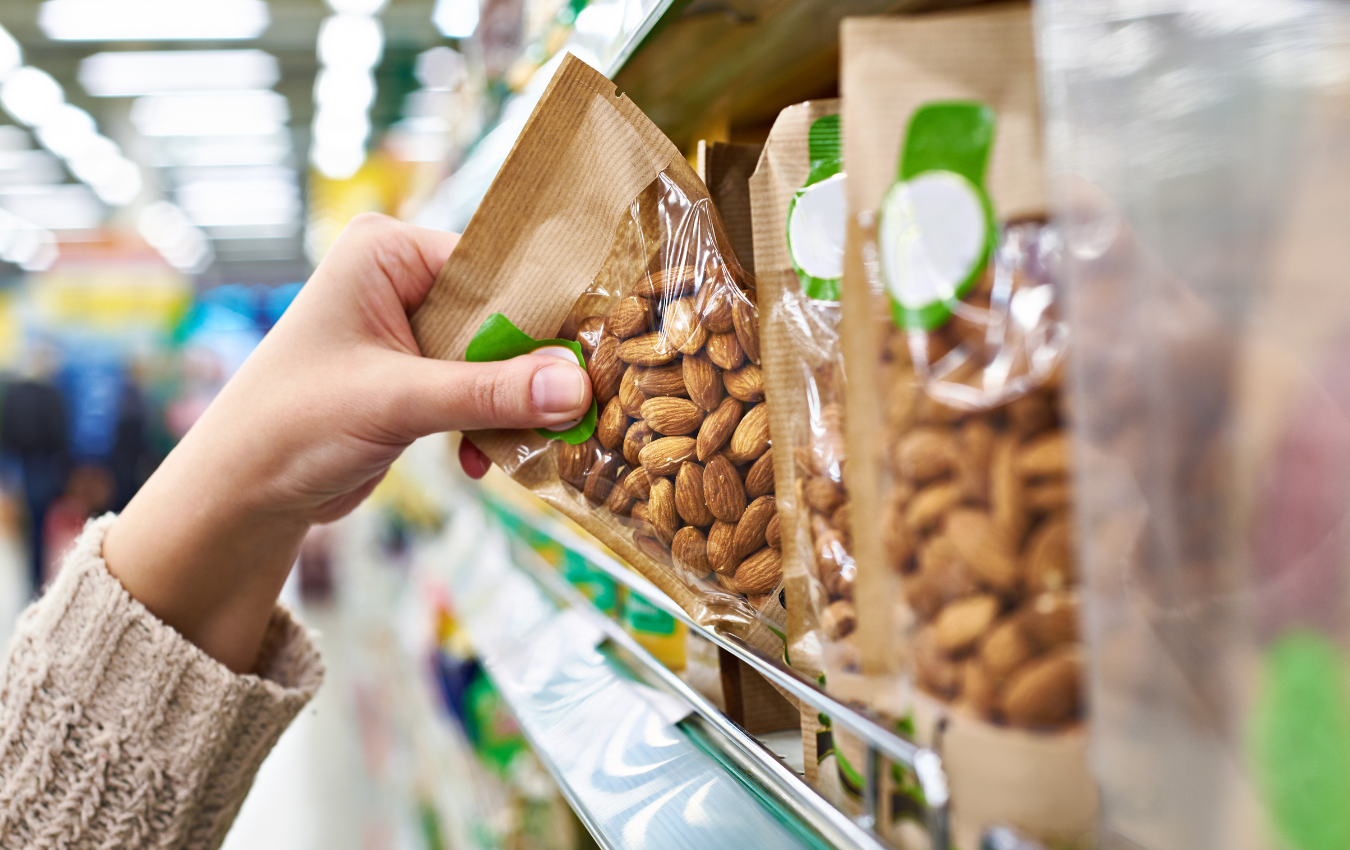
The flexible packaging industry is experiencing a significant evolution as it leans into more sustainable practices. Amid growing environmental concerns, there’s a strong movement within
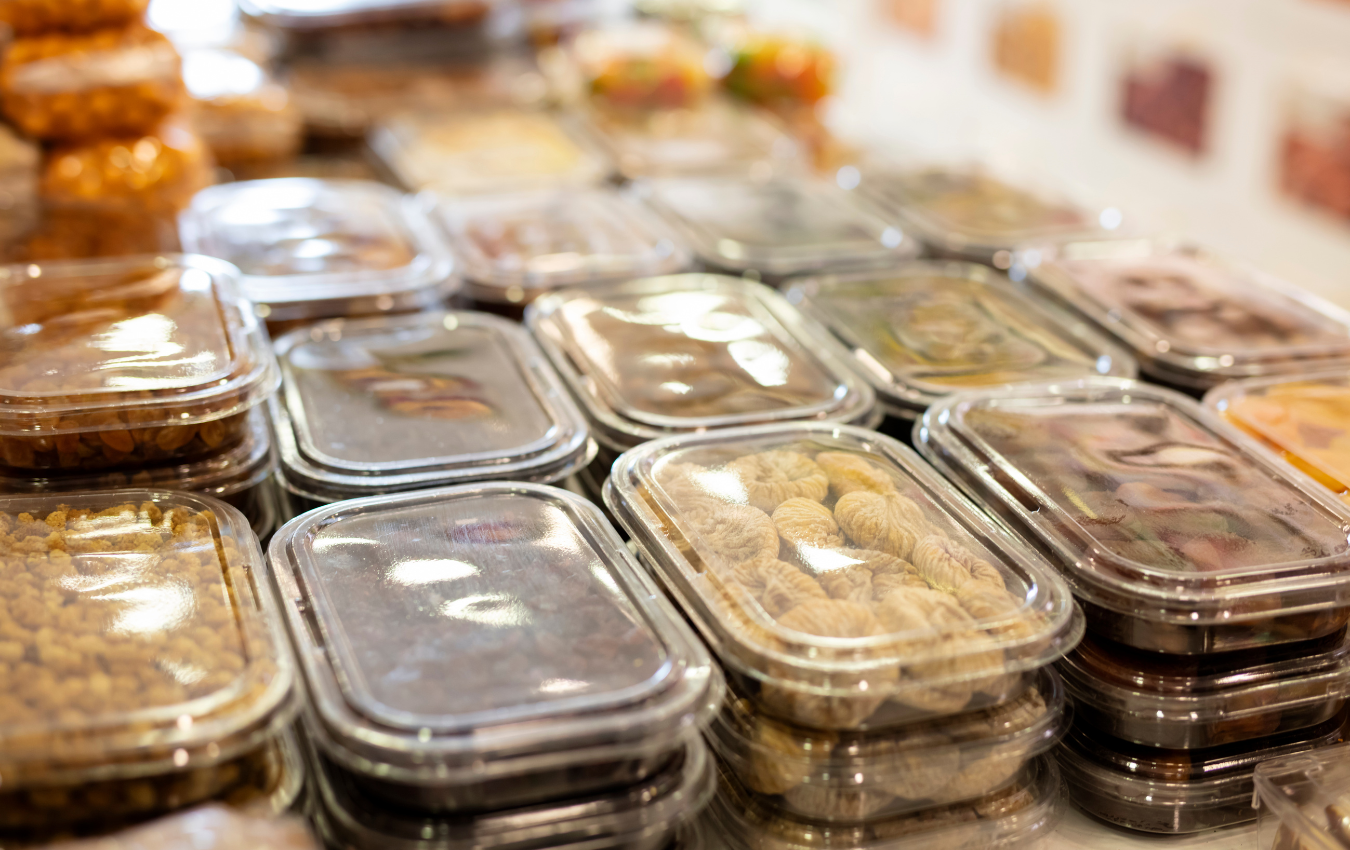
The world of packaging has seen tremendous innovation over the years. With the increasing emphasis on product safety, hygiene, sustainability, and overall aesthetic appeal, manufacturers