Home » Mastering Quality Control in POP Production
Mastering Quality Control in POP Production
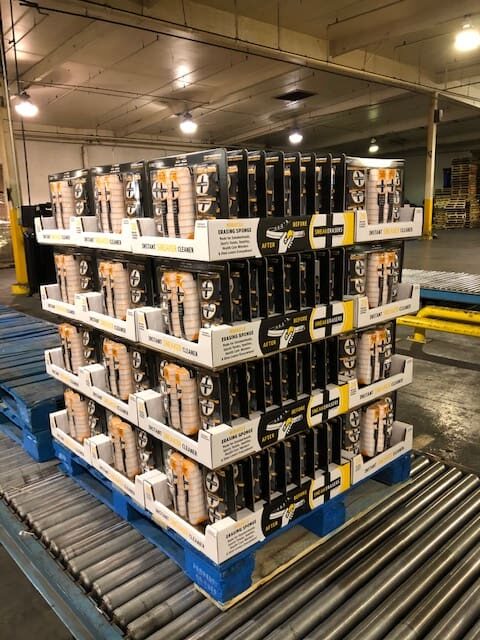
Once the design and material selection for a Point of Purchase (POP) display are locked in, the project moves into the critical production phase. This stage is where your concept is transformed into a tangible product ready for retail environments. The key to successful production lies in stringent quality control measures and a well-coordinated manufacturing process. This blog outlines the essential steps and considerations for the production phase of POP displays, ensuring each unit is built to meet both aesthetic and functional standards.
Streamlining the Manufacturing Process
Setting Up the Production Line
The first step in the production phase is setting up the manufacturing line. This setup should be optimized based on the design specifications and material requirements of the POP display. Efficient line setup helps minimize production time and cost, ensuring that each component is assembled correctly and efficiently.
Integrating Technology and Automation
Where possible, integrating advanced manufacturing technologies and automation can enhance precision and speed in the production process. Automation can be particularly beneficial in producing components that require consistent replication of detailed designs, contributing to uniformity and quality across all units.
Implementing Quality Control Measures
Developing Quality Standards
Before production begins, establish clear quality standards that align with the display’s design and functionality goals. These standards should cover all aspects of the display, including material integrity, color accuracy, structural stability, and overall finish.
Continuous Quality Monitoring
Implement continuous quality monitoring throughout the production process. This involves regular inspections and testing of the displays at various stages of manufacturing. By catching defects or deviations early, you can prevent issues that might compromise the final product’s effectiveness.
Feedback Loop with Design and Materials Teams
Maintain a feedback loop with the design and materials teams. This collaboration ensures that any potential issues identified during production can be traced back to design or material choices and addressed promptly, preventing recurrence.
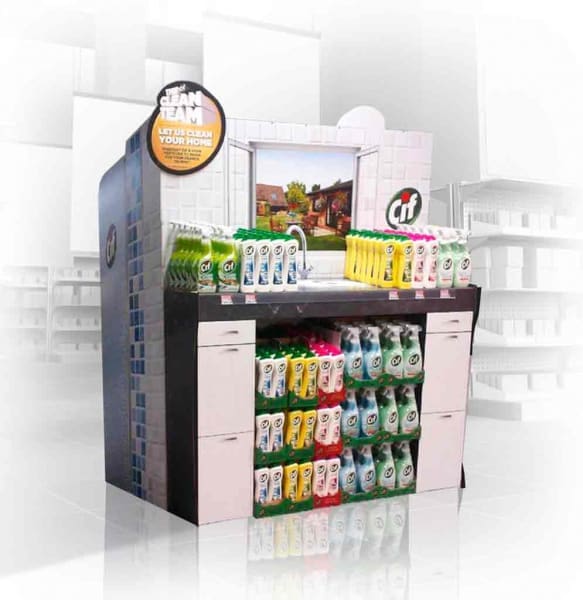
Ensuring Compliance with Specifications
Adherence to Design Specifications
It’s crucial that the manufacturing process adheres strictly to the agreed-upon design specifications. This adherence prevents variations that could affect how the display performs in its intended retail environment and ensures that all functional and aesthetic elements are preserved.
Alignment with Material Specifications
Similarly, ensure that the materials used in production match the specifications decided during the planning phase. Using the correct materials affects not only the display’s look and feel but also its durability and impact in a store setting.
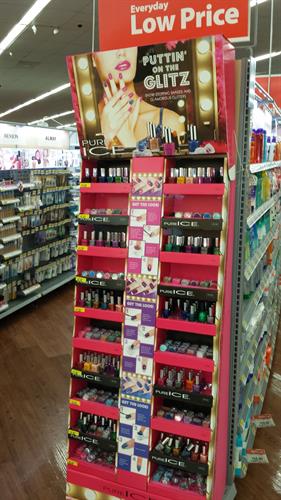
Preparing for Post-Production
Assembly and Pre-Installation Checks
If the display requires assembly post-production, conduct thorough checks to ensure all parts fit together correctly and that assembly is as straightforward as possible. These checks can help streamline the installation process later on.
Final Quality Assurance
Before the displays are shipped, a final quality assurance check should be conducted. This final review ensures that every display unit meets your brand’s quality standards and is ready for deployment without needing further modifications.
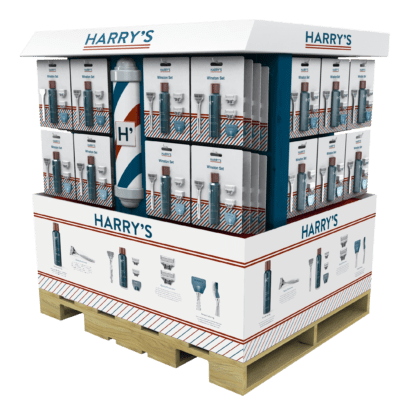
Conclusion
The production phase is where your POP display comes to life. By focusing on efficient production setups, stringent quality control, and strict adherence to specifications, you can ensure that the manufactured displays meet the desired standards. Thorough planning and monitoring during this phase lay the groundwork for effective POP displays that attract attention and withstand the demands of the retail environment, ultimately driving sales and enhancing brand presence.
If you are interested in POP displays, then partner with Brown Packaging today to get started.
Rigid boxes are the gold standard of premium packaging. Whether used for cosmetics, electronics, fashion, or high-end subscription kits, rigid boxes do more than protect your product—they create a lasting
Understanding One-Piece FOL and Three-Piece Bike Shipping Boxes Choosing the right box style is essential when shipping bicycles—especially for brands, manufacturers, and distributors focused on protection, cost efficiency, and streamlined
Corrugated boxes are essential to shipping, retail, and e-commerce—but when you introduce custom printing, the stakes (and the opportunities) rise. Print isn’t just about looks—it’s about communication, branding, compliance, and
When it comes to shipping bikes, selecting the right type of corrugated box is essential to ensure product protection, ease of handling, and cost efficiency. Two of the most common
Home » Mastering Quality Control in POP Production