Home » Direct Thermal vs Thermal Transfer Printing: What is the Difference?
Direct Thermal vs Thermal Transfer Printing: What is the Difference?
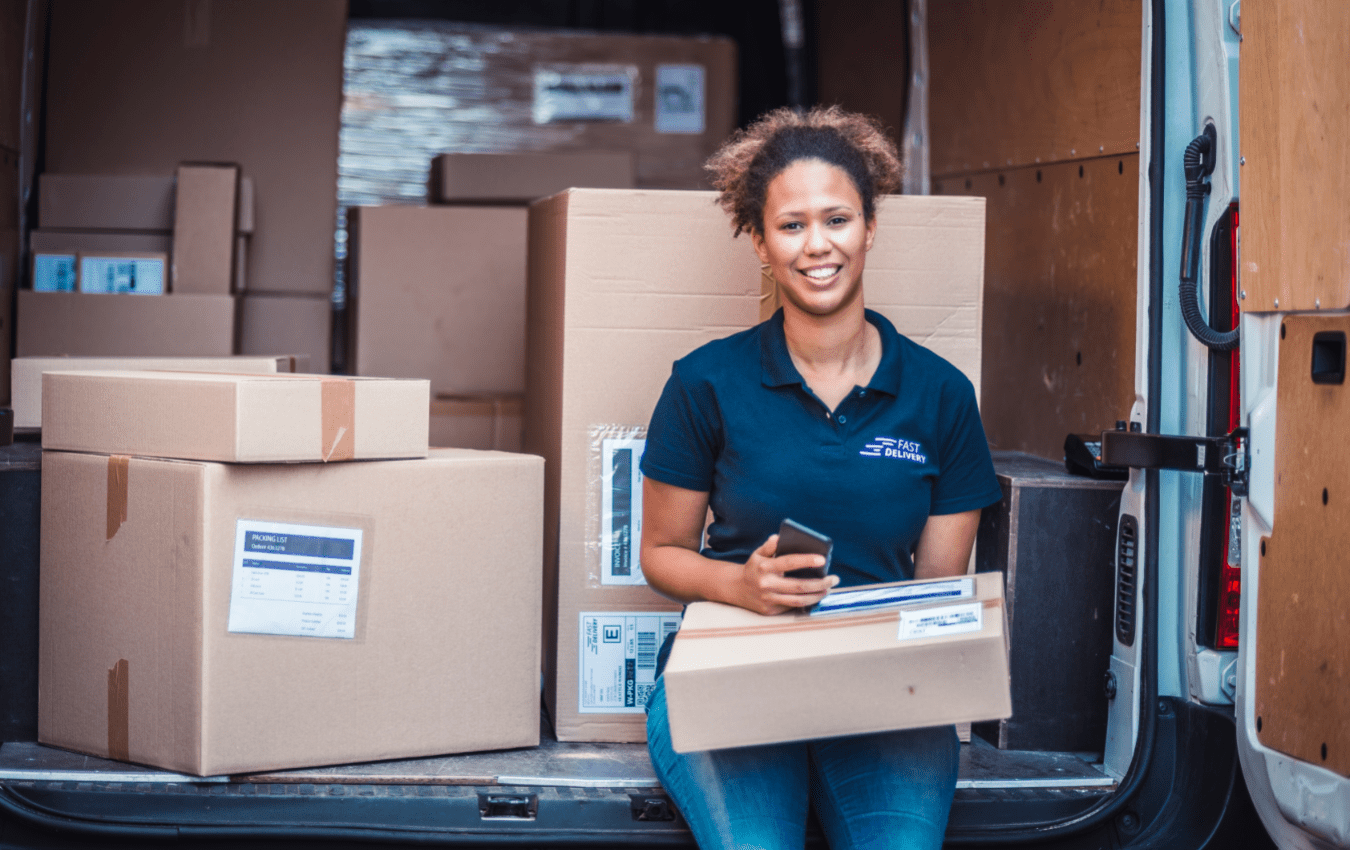
Direct thermal and thermal transfer are similar in the fact that they are both ideal choices for printing information on labels such as barcodes, however they can differ in their printing process and labeling applications based on their attributes, advantages and disadvantages. By identifying and understanding the key differences between the two, you can pick the best labeling solution for your business.
Direct Thermal Printing Explained:
Direct thermal printing process applies heat sensitive chemicals to media, which blackens as it passes under the thermal printhead, essentially creating the image or barcode. This method is popular among so many as it offers simplicity by not requiring any ink, toner or ribbons. In addition, these labels are printed with high quality and scan-abilitty.
Labels printed as direct thermal tend to have a short term shelf life as the chemicals used to produce print are highly sensitive to environmental conditions. For example, abrasion, sunlight and heat can cause the material to darken and become unreadable. Essentially, the shelf life of these labels will depend on your labels’ handling and environmental conditions.
For these reasons, many buyers have to weigh their options on whether direct thermal printing is the best solution for them. Direct thermal printing offers a smooth and simple application process at the expense of shelf-life and environmental vulnerabilities. As a result, consider the advantages, disadvantages and applications of direct thermal labels before you buy.
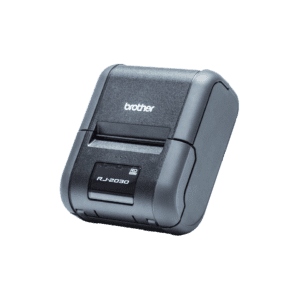
Direct Thermal Mobile Printer
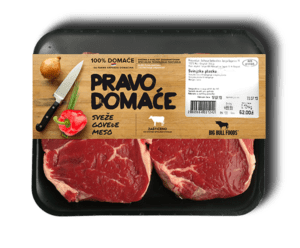
Direct Thermal Printed Label
Direct Thermal Advantages
- Sharp and high quality prints which makes it an ideal choice for scannable barcodes
- Ideal for short-term applications, does not produce waste
- Sustainable solutions are available
- Ease of use and simplicity of creating labels
- Does not require ink, toner or ribbon
- Low maintenance
- Paper and synthetic material options available
- No setup time
Direct Thermal Disadvantages
- Sensitive to environmental conditions such as light, abrasion and heat
- Not ideal for long term label applications
- Often require resistant coating of UV light, chemical and abrasion
- Chemical used for direct thermal remains active
- Quality and durability is not as good as thermal transfer
- Can fade within 6 to 12 months
Direct Thermal Applications
Direct thermal should be used for short to medium term applications and are often printed individually or through batches. They are typically used as shipping labels, receipts, visitor identification, meat carton labels, tags, inserts and cards, price weigh retail labels and ticket printing applications. In addition they are reliable for office and industrial operation labeling applications.
These labels are not recommended for products. For example, a retail box barcode will undergo a variety and vigorous amount of supply chain events, which makes direct thermal applications not suitable.
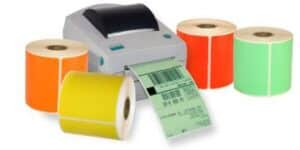
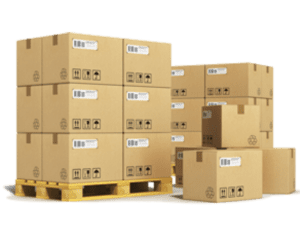
Thermal Transfer Printing Explained:
Thermal transfer printing method, which requires a ribbon roll to be heated by a printhead that melts ink onto the label, creating the image, where it is absorbed into the media. Since ink is absorbed, the image cannot be rubbed off, which makes these labels highly durable. These labels make printed surfaces appear glossy and crisp, and provide users with quality and reliable labels.
Thermal transfer printing requires more of a technical set up to print your ideal label, as material, ribbons and adhesives must be matched to get the desired performance and durability. Essentially, these labels will be resistant to environmental conditions such as sunlight, inclement weather conditions, chemicals, sterilization and more. In addition, Color and density can vary depending on the ribbon and the resolution of the printer.
However, you may be wondering if all this effort purchasing ink, ribbons and toners is worth it. Before you make a purchasing decision checkout the advantages, disadvantages and applications of thermal transfer printing.
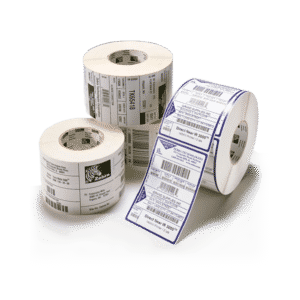
Thermal Transfer Labels
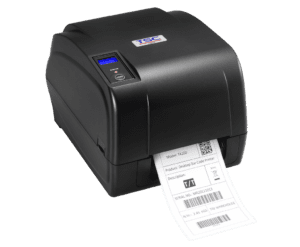
Thermal Transfer Label Printer
Thermal Transfer Advantages
- Superior quality prints with high definition text, graphics and barcode for best scan-ability and readability
- Shelf-life is long-term
- Can be used for 1D and 2D barcodes
- Does not create waste
- Colored ribbons are available
- Best for small text
- Durable in extreme temperatures, moisture, UV exposure, sterilization, chemicals and other environmental conditions
- Higher speed printing
- Longer print head life
Thermal Transfer Disadvantages
- More costly to produce than direct thermal
- Not sustainable friendly
- Ribbon and media must be compatible
- Requires maintenance/resupply of ink, ribbon and toner
- Requires setup and ribbon change overs
- Ribbons can wrinkle and damage print quality
Thermal Transfer Applications
Thermal transfer labels are used in a wide variety of long term applications such as product identification, inventory identification, shipping labels, certification labels, sample and file tracking, permanent identification, circuit board tracking, cold storage, outdoor applications, laboratory specimen identification, and more. In addition, thermal transfer labels are used frequently in industrial environments to label hazards, directions and chemicals.
These labels are not recommended for short to medium term applications as it can be done more cost effectively and quickly with direct thermal printing.
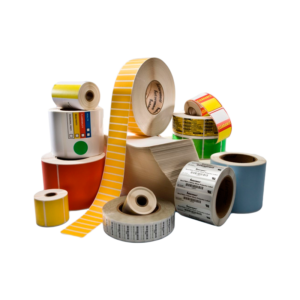
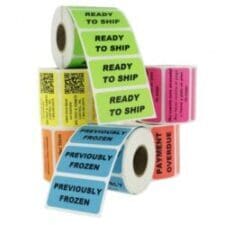
Why Board Grade Selection Matters In today’s volatile supply chain environment, packaging failures aren’t just a nuisance—they’re a liability. Damage in transit, product returns, and
Why Holiday Fulfillment Demands Precision The holiday season introduces a unique set of pressures across the packaging and supply chain landscape—especially for businesses managing kitting,
Why Custom Corrugated Boxes Remain a 2026 Essential Custom corrugated boxes continue to be the most relied-on packaging solution for industries ranging from industrial manufacturing
Why Co-Packaging Becomes Critical During the Holidays As the holiday season approaches, packaging teams are under pressure to deliver high volumes of promotional sets, combo
Holiday demand starts long before December. So should your packaging. For B2B and D2C brands alike, Q4 is the most critical—and most chaotic—shipping window of
The Challenge of Multi-SKU Holiday Programs During the holiday season, brands often shift from selling single products to curated sets, bundled assortments, and promotional kits—each
Home » Direct Thermal vs Thermal Transfer Printing: What is the Difference?
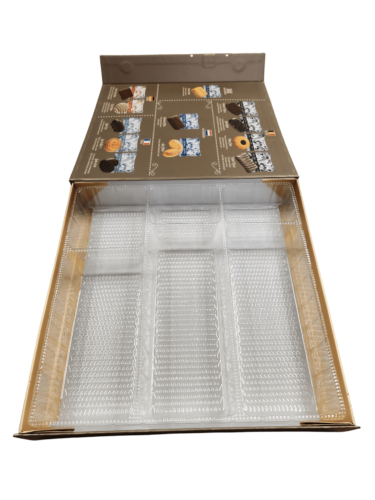
In the dynamic and ever-evolving food industry, packaging plays a pivotal role in preserving the quality, safety, and freshness of products while also captivating consumers
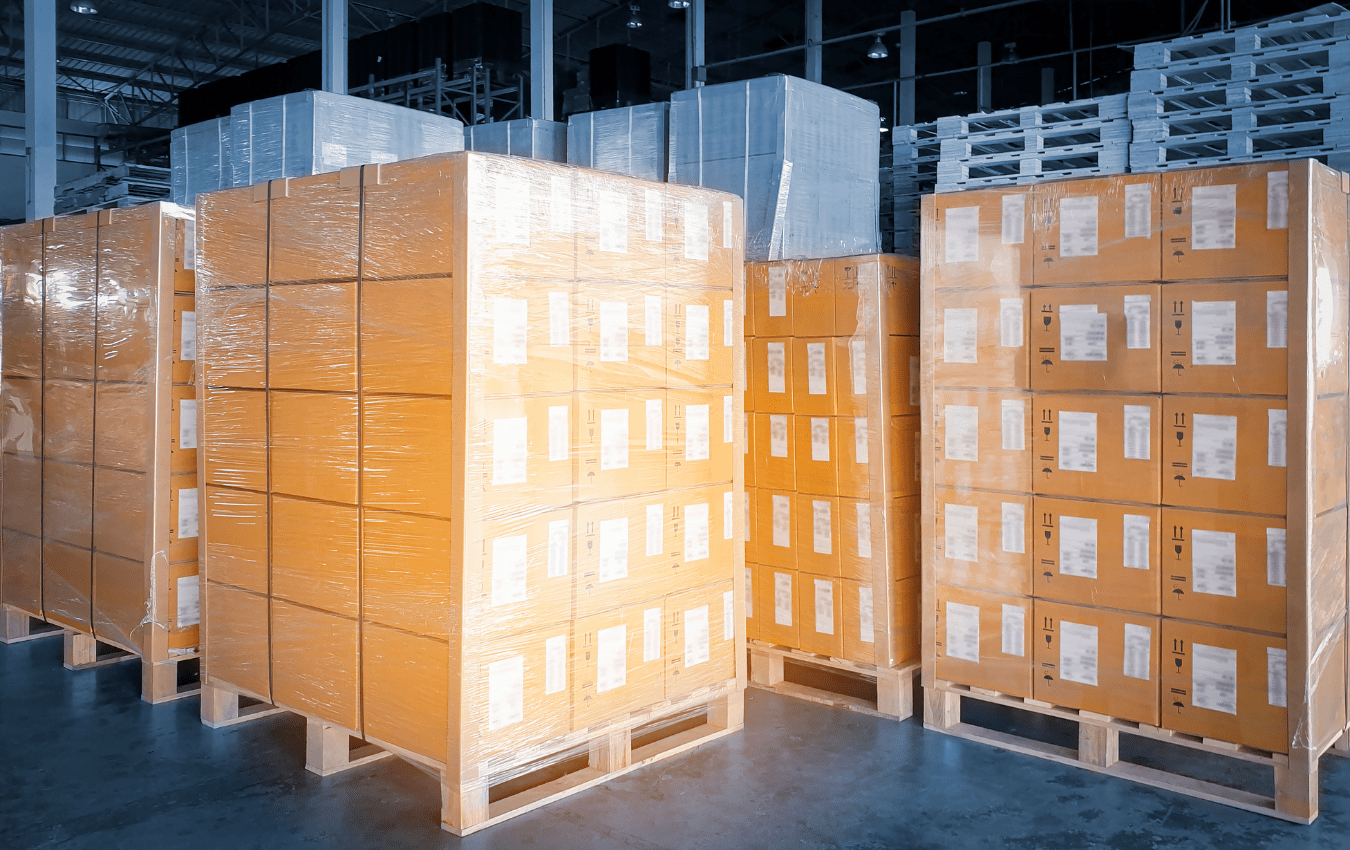
When it comes to packaging fragile or valuable items, ensuring their safe transportation is crucial. One effective way to protect these items during shipping or
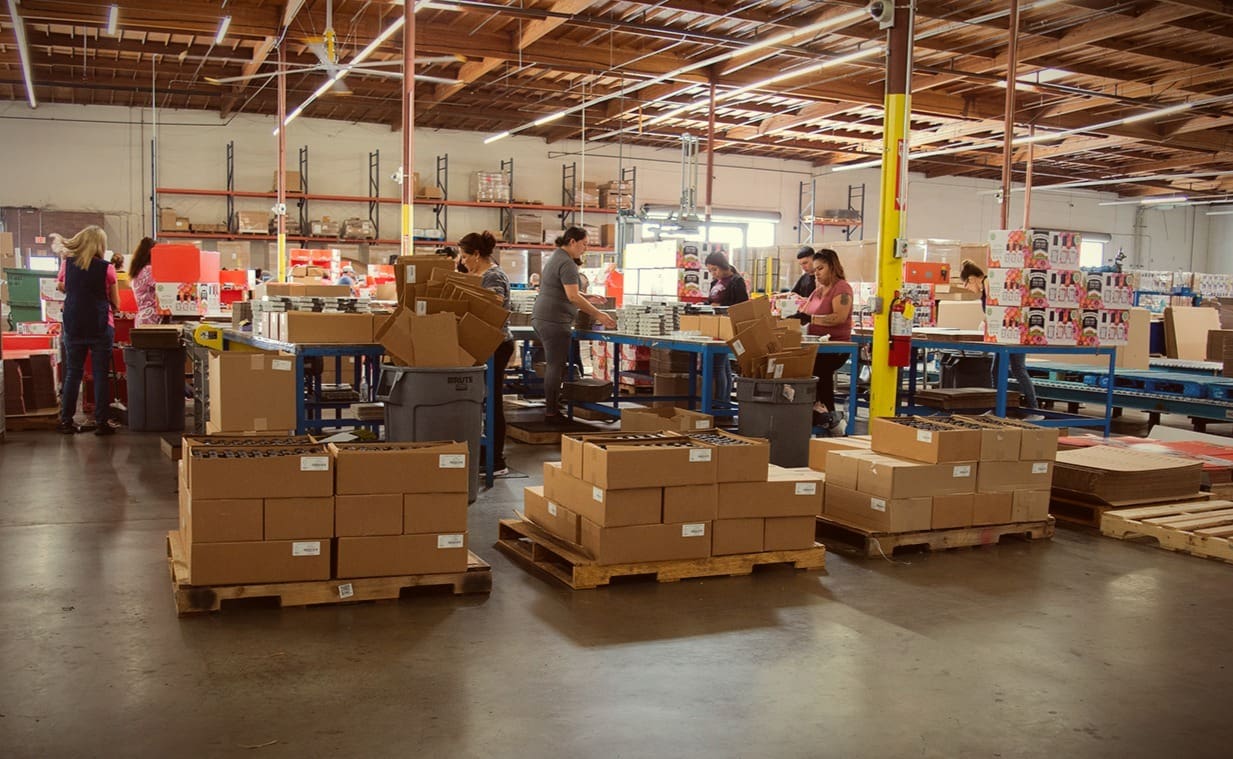
The retail landscape is in a constant state of evolution, shaped by dynamic consumer behaviors and emerging trends. As consumer preferences continue to shift, retailers